About Fields Pottery
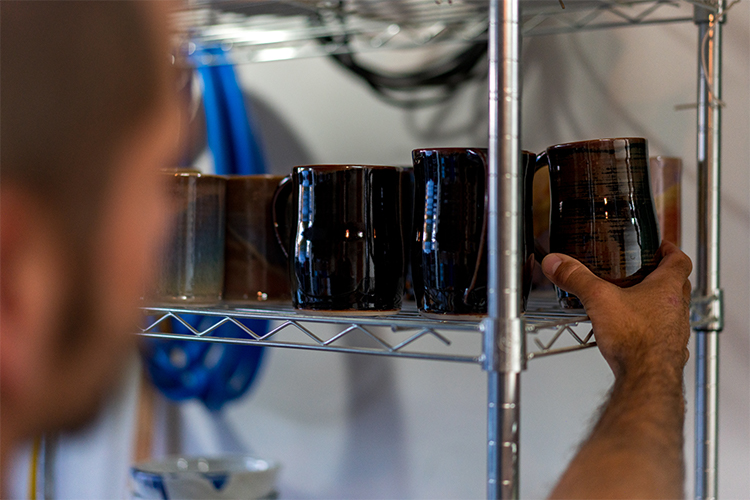
Converse Fields fell in love with clay at an early age when his parents would bring him to art classes in his hometown of Northampton, Massachusetts. He later discovered the potter’s wheel while attending Holderness School, and became equally fascinated with creating glazes.
Holderness ceramics instructor and artist-in-resident, John Swift, shared his passion for pottery, and his years of knowledge as a professional potter in Colorado and California.
After graduating from Holderness, Converse’s love for working with clay was put on hold while he pursued a career as a professional snowboard racer. For the next 10 years Converse competed on the FIS World Cup, World Championships, European and North American Cups.
Today, he is happy to be settled in Steamboat Springs, Colorado with his daughter, Adeline, and wife, Crystal.
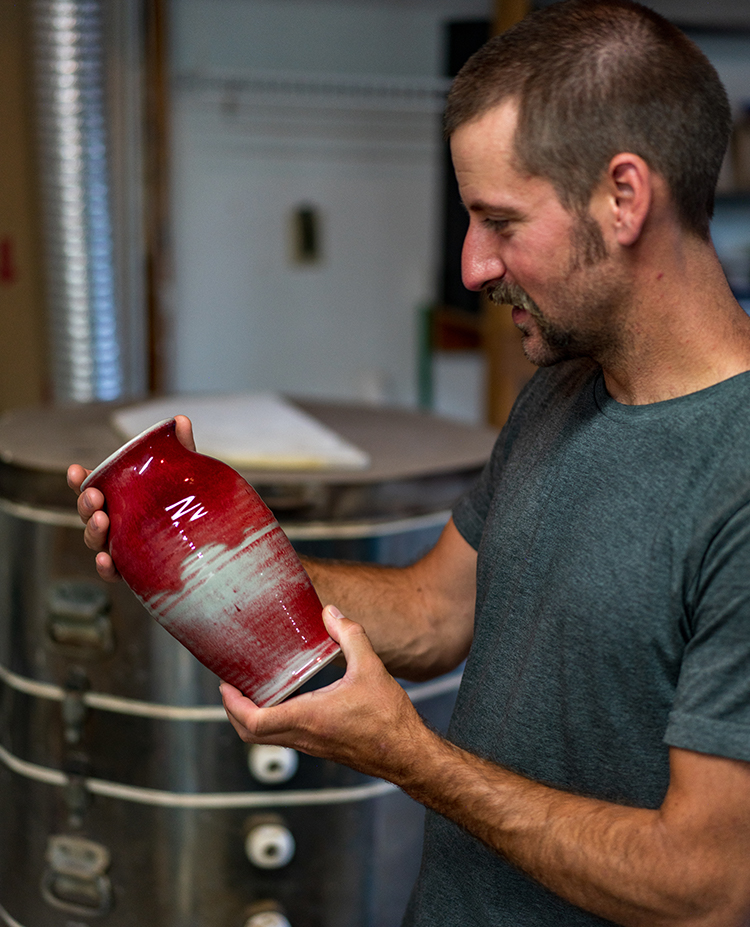
When it was time to start Fields Pottery, Converse reached out to John Swift who graciously passed along hundreds of glaze recipes and numerous other business and production notes. Even with these notes and recipes, variations in materials, kilns, altitude, and styles led to countless hours of testing before the first Fields Pottery pieces were completed.
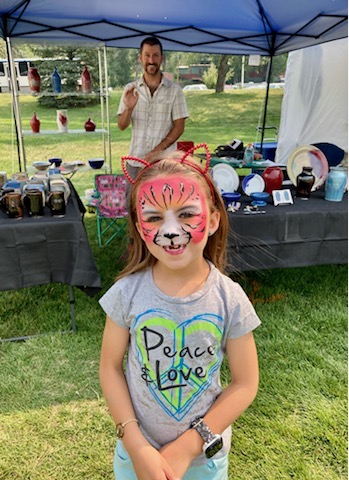
Converse’s eight year old daughter, Adeline, loves to work with clay, too.
Today, Adeline has a few bags of porcelain that weigh more than she does…but not for long. When she’s not rock climbing or skiing with her family you can find Adeline singing a happy tune while creating her cats!
About The Process
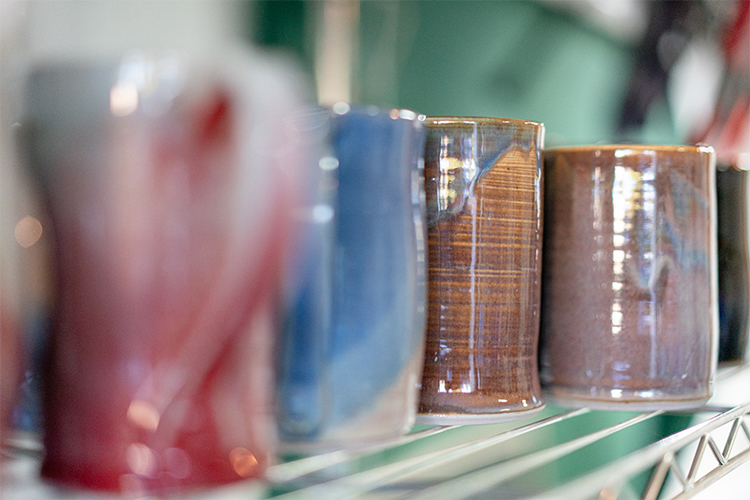
All of Converse’s fine hand crafted pottery is made using grolleg porcelain.
You may notice different colors in the clay body depending upon where they were positioned in the kiln during the glaze fire. Pieces that are fired in reduction tend to be gray, whereas the pieces fired in oxidation are light tan to white.
Converse enjoys the chip resistant, durability and appearance of porcelain.
Each piece is thrown on the potter’s wheel. All handles are pulled by hand. Every piece is unique, which is why you will notice small variations even in matching sets.
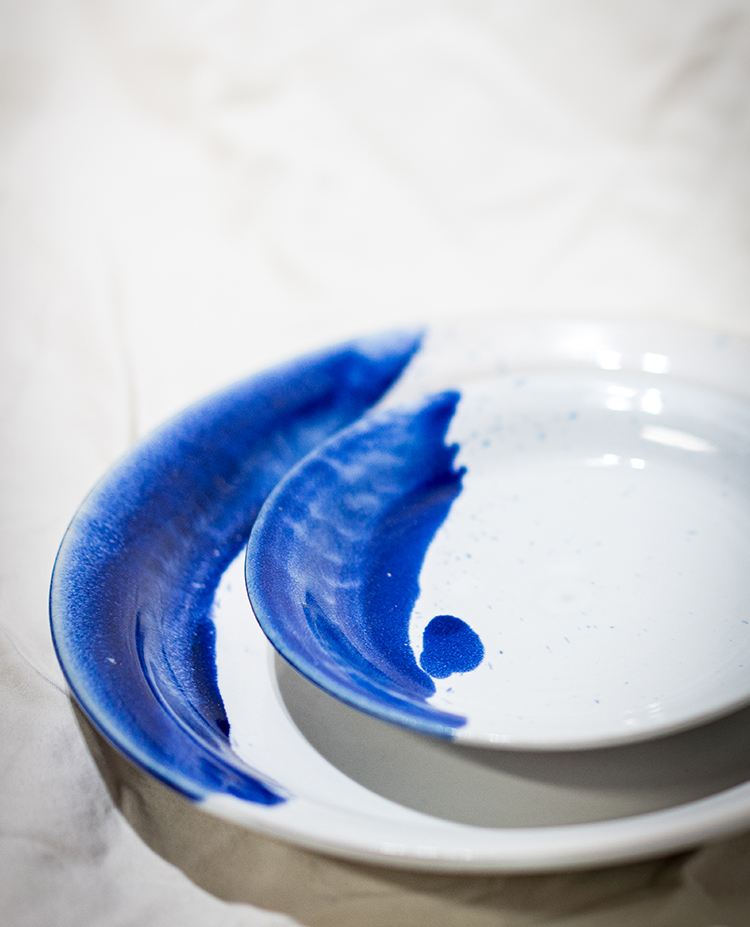
The glazes are all painstakingly measured, tested, and mixed from powdered minerals and oxides.
All glazes used are food safe.
Most of the glaze recipes have come from Converse’s friend and mentor, John Swift, but due to changes in availability of materials over the years, all of these materials have been adjusted to create stable glazes with modern supplies. These adjustments are done through a long process of trial and error.
Each piece is fired twice
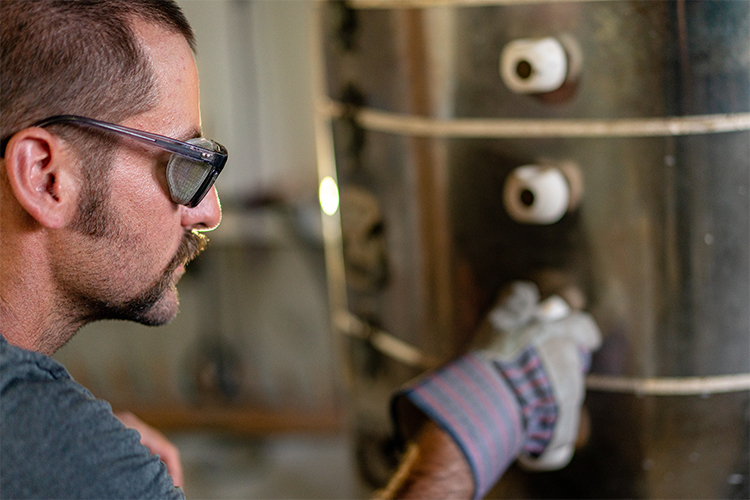
After a piece is thrown, trimmed, and handles attached, it is dried fully before being loaded into the kiln for the bisque fire. The first firing reaches around 1950 degrees f. The high heat burns out organic matter in the clay, but keeps the (now ceramic) material porous, making it much stronger than before.
The bisque ware is then glazed and fired again to cone 10 (around 2300 f).
A gas kiln allows Converse to make adjustments in the atmosphere. While some of his glazes come out better in an atmosphere with adequate oxygen for complete combustion (oxidation) most of Converse’s glazes are developed for a reduction atmosphere, in which the kiln is starved of oxygen for much of the firing.
The atmosphere is carefully adjusted throughout the firing.
Pieces must be placed in certain zones in the kiln for the desired effects.
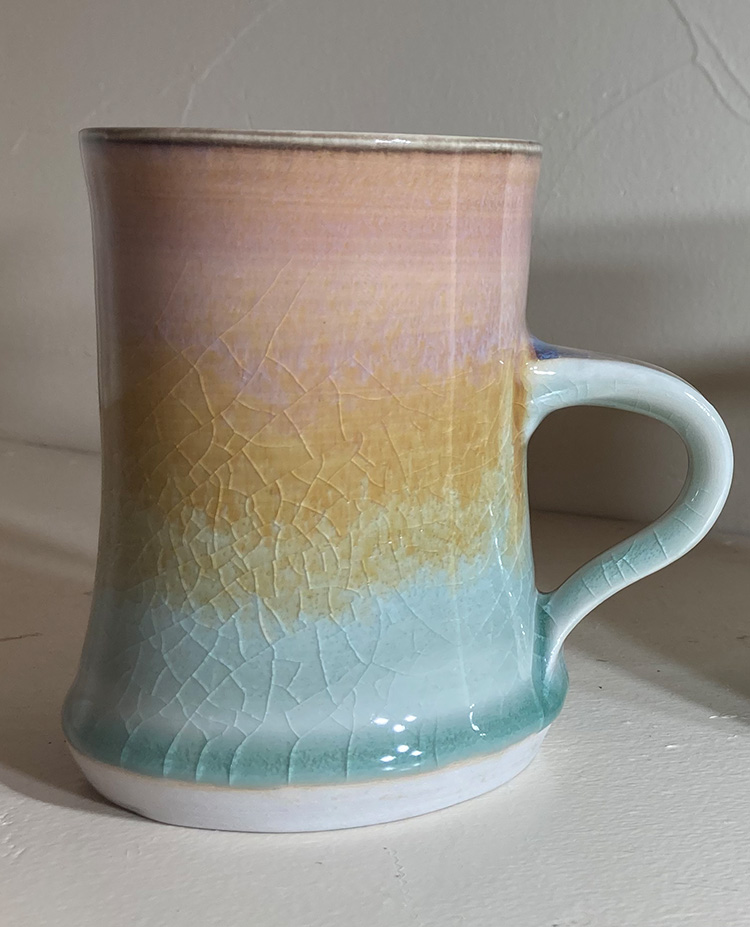
If a piece is placed by an air draft, it can create an unexpected and wonderful surprise effect.
Copper Red
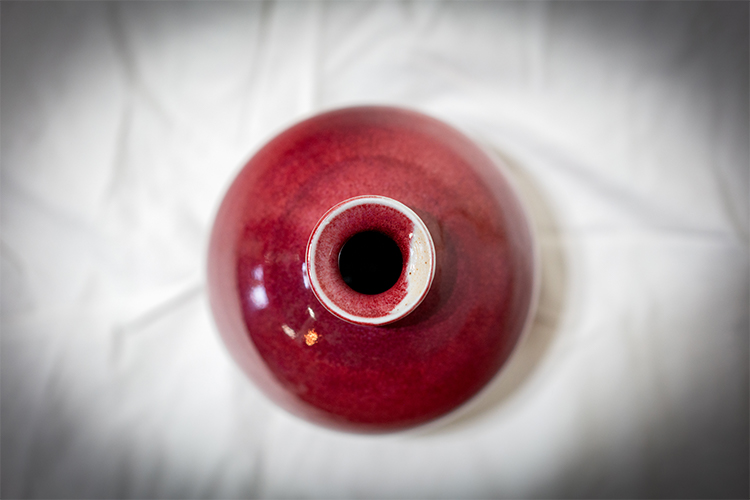
The most notable of the glazes affected by the reduction atmosphere is copper red. If proper reduction is not achieved, these beautiful reds come out green or light blue instead.
Tenmokus and Celadons
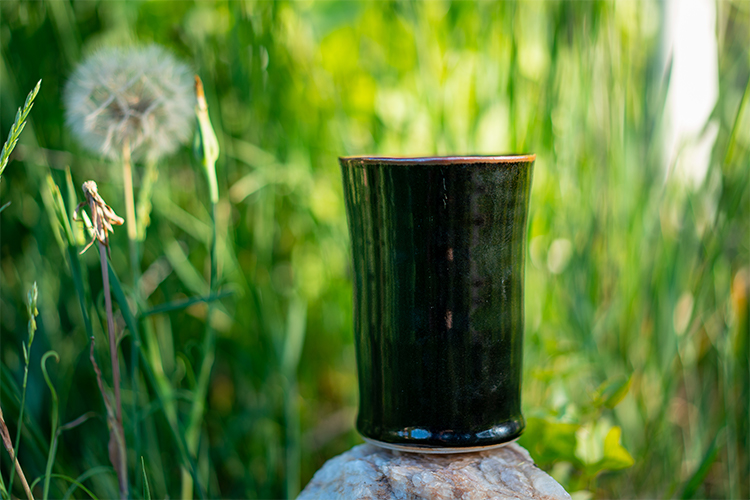
Tenmokus, celadons, and even rutile blue and tan glazes are also greatly affected by the atmosphere.
Adeline’s Cats
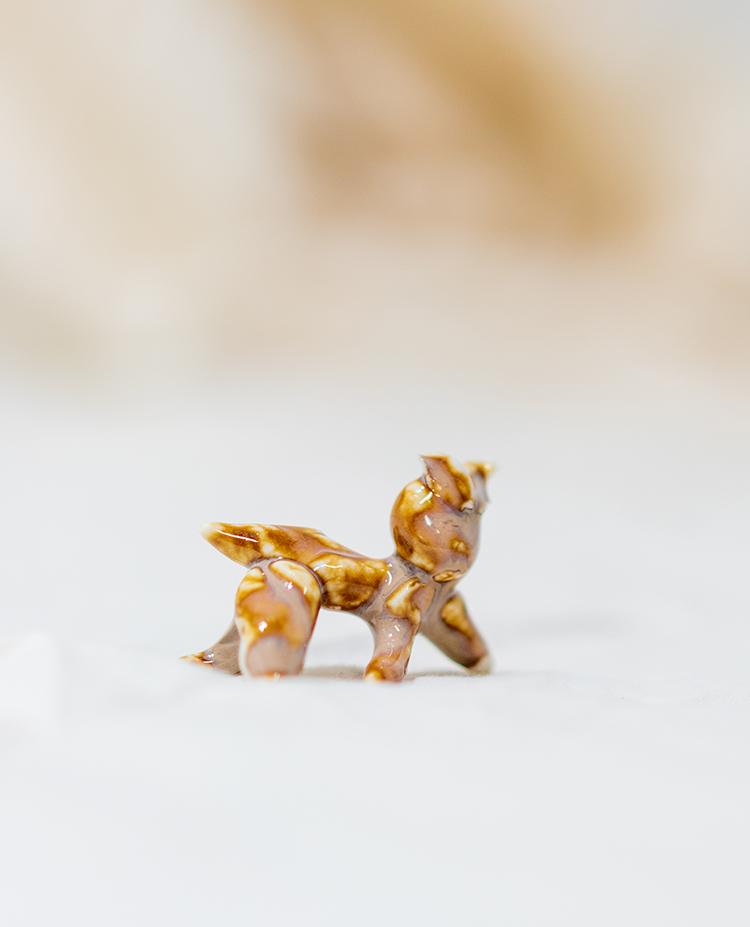
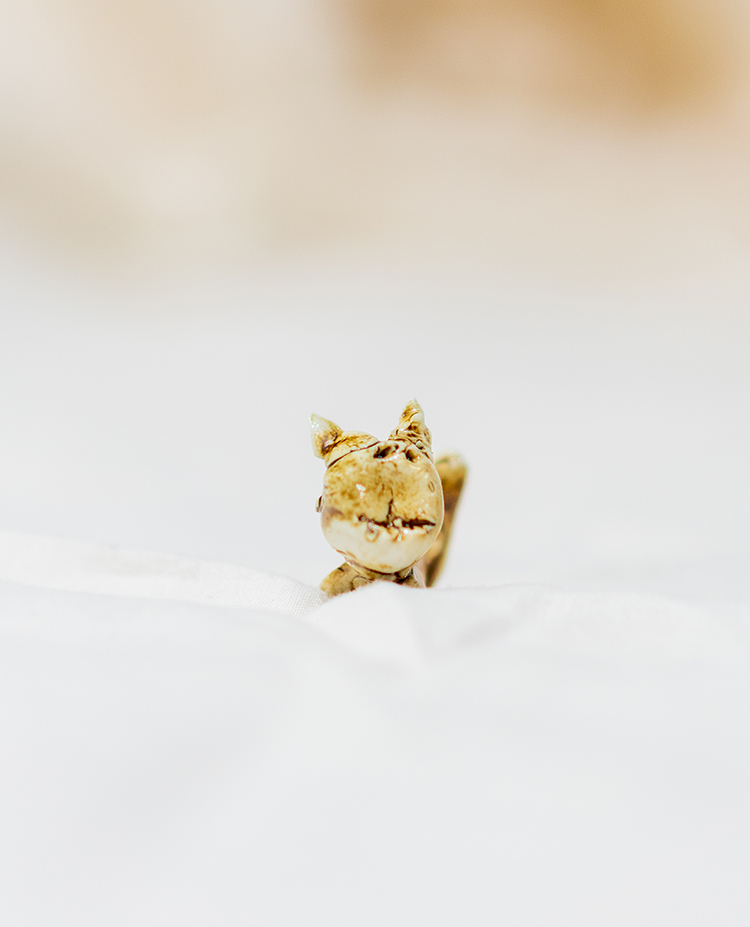

Adeline’s Cats are made using the same glazes and firing methods that Converse’s employs. Most of her cats are inspired by her cat, Jah Rastafurri. She also picks up ideas and inspiration from the world around her to make every cat fun and unique.